The ingredients necessary to manufacture a product are called the Bill of Materials, or BOM. As such, effective BOM management is a critical component of the product lifecycle management (PLM) process. This article explores the best practices for bill of materials management so that you can get the most out of your PLM software. But before we delve into the best practices, we will try to understand what is BOM first.
Let’s get into PLM BOM.
What is a Bill of Materials (BOM)
The most common question, what is BOM management, requires special attention because it serves as the basis for understanding the practices. A bill of materials (BOM) is a comprehensive list of items, parts, assemblies, and other materials necessary to create a product, as well as the instructions required for gathering and using the materials needed. Consider the agile bill of materials as the shopping list and recipe for building the end product. In addition, a bill of materials program is intended to assist in effectively managing and arranging BOM data.
BOM is sometimes alternatively known to be a product structure or production receipt because of the nature of its contents. These BOMs usually follow or carry a structure where the opposite ends contain raw material and the finished product at the end. Fascinating, isn’t it? Comprising product codes, descriptions, costs, specifications, and quantities, it represents everything a product receipt should have.
Being the foundation of a production system, it is an integral part of the PLM process. With instructions on how to use the contents of BOM inventory management, it leaves no room for confusion regarding the procurement and usage of each item. For ease of use, one can store the information or production receipt like that of the bill of material on a spreadsheet, ERP, or PLM. Additionally, BOM DMS (Document Management System) can be utilized to structurally store documents, drawings, and files throughout the product lifecycle. It is an effective way of keeping data up to date.
What is the BOM Management Process
BOM management or bill of materials management refers to handling, capturing, managing, and configuring product data of a given product lifecycle. It should be noted that the Bill of Materials is not a tricky concept. BOM management in agile PLM could be understood through the following:
Here’s a list of common BOM management representation methods. These BOM methods are critical in production and inventory control.
- Single-level BOM
- Multilevel BOM
- Engineering BOM (EBOM)
- Manufacturing BOM (MBOM)
- Production BOM (PBOM)
- Configuration BOM (CBOM)
- Service BOM (SBOM)
- Variant BOM
- Master BOM
Elements to Add to an Effective BOM
One of the main goals of BOM (bill of materials) is to ensure that you build the product right. Therefore, you need to include certain pieces of product information in the BOM management software record, and bills of material should mention specifications too.
Irrespective of whether you want to create your first BOM management or improve an existing agile bill of materials, you should include the following list of product-related information in your BOM management software record.
BOM Level | Unit of Measure |
Part Number | Procurement Type |
Lifecycle Phase | Reference Designators |
Description | BOM Notes |
Quantity |
Which is an effective BOM: 100%, 120%, or 150%?
100% BOM
100 % BOM is a completely useful BOM for making the finished product. We can manufacture at 100% BOM, meaning there’s no additional information about the product. It also means that no alternative option exists on any part of the product.
The following figure shows 100% BOM information of the Pen product. In the figure, only one option is available for a front cover, rubber strip, and ink color. We can go with this option of the bill of materials for manufacturing the Pen.
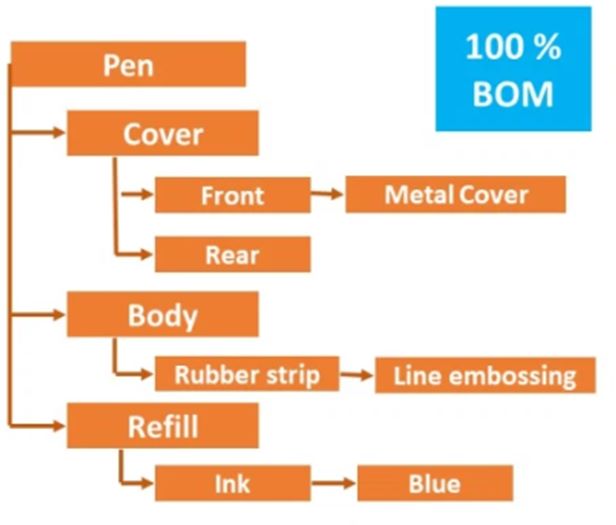
120% BOM
The 120% bill of materials (BOM) can only provide incomplete BOM management in PLM details for a part, it cannot be used to construct the final product. To create the finished product, it is necessary to convert the 120% BOM into a 100% BOM.
The 120% BOM shows two ink options: red and blue (this is the additional information) in the below figure. We must choose either the blue or red option in the bill of materials to start the manufacturing process, this is the conversion of 120% BOM into a 100% BOM. Make sure in the end all 150% BOM transforms into 100% for better results because 150% BOM does not work in our favor.
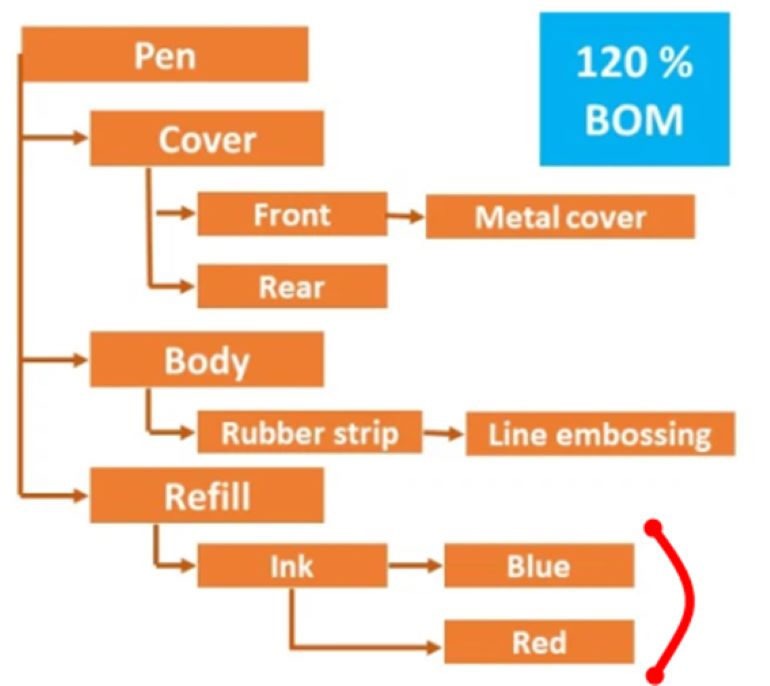
150% BOM
The BOM (bill of materials) contains all alternative parts; full overlays of parts are known as 150% BOM. 150% BOM is also unsuitable for creating the final product, just as 120% BOM is unsuitable for the same purposes. You have to convert it into a 100% BOM.
The following figure shows 150% BOM. There are two options for the front cover (metal and plastic), two options for rubber strips (dotted and lined), and two options for ink color (blue and red). We have to select one option from each alternative to make a final product. In short, we have to convert it into 100% BOM. This is what a 150% bill of materials is.
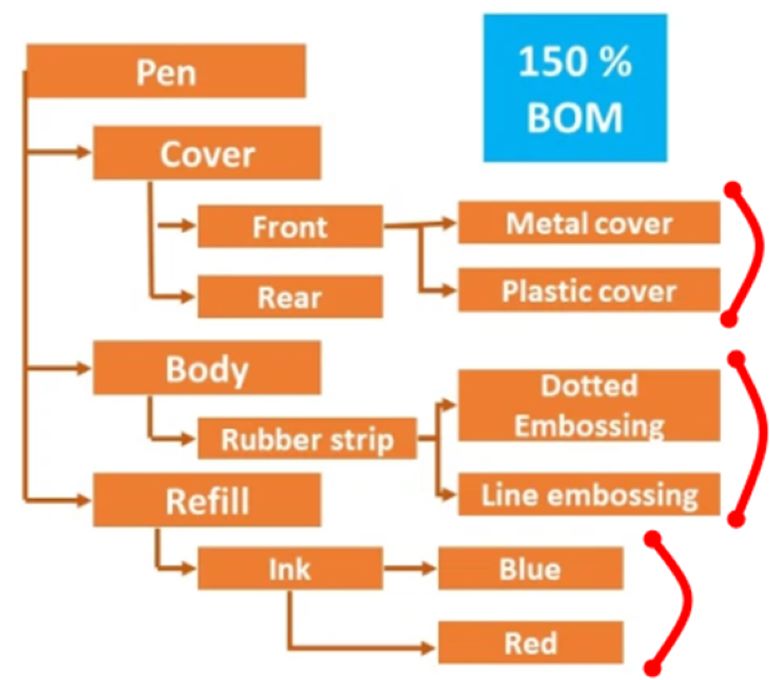
Key Questions to Answer When Creating a BOM
Creating a bill of material management process requires certain information.
Here’s a list of questions you should ask to gather the relevant information.
- Are There Consumables That Need to Be Itemized? Sometimes, manufacturers fail to include mass-quantity consumable items—such as glue, wires, fasteners, labels, and boxes—in the BOM. All the necessary materials must be included in your BOM process for it to serve as an accurate procurement and production document.
- Are There Any Files That Must Be Attached to Your BOM? You need to append many BOMs processes or bills of material management process with supporting documentation, such as computer-aided design (CAD) drawings, part datasheets, and subassembly instructions. Make sure any attached files are correctly matched to specific BOM-level items.
- Who Will Use the bill of material management process? You should take into account any team or member of a team who might need access to the BOM. Therefore, you should ensure the BOM carries all the information a stakeholder might require throughout the manufacturing and packaging product lifecycle management.
- How Will You Track BOM Revisions? BOMs often go through several changes during the design phase. Therefore, you must determine a way to identify the different BOM versions and make a distinction between them. This practice will help you ensure that everyone is referencing the correct version when production begins.
5 Fundamentals of a Successful BOM Process
You should implement and enable BOM processes in a way that ensures they are:
- Accurate
- Current
- Complete
- Clear
- Actionable
Aim for Accuracy
Provide Accurate Data Downstream
Manufacturers use their BOM to inform the downstream operations on what they need to execute. Providing accurate information to other teams and employees is crucial; otherwise, your downstream operations team could order the wrong parts or produce an incorrect revision. Bill of materials acts as a guide for engineering teams and product development teams.
Get Data from the Source
Companies must ensure that their information is correct and to the point. But how do they do that? To begin with, you should collect existing data directly from the source rather than entering it manually. When it comes to BOM data BOM management, it implies the metadata and product structures from CAD tools to record the engineer’s intent. Besides the initial collection of this data, you must also keep it synced as designs change frequently.
Allow Visibility and Collaboration
Next, you should ensure BOM management that information is available and visible to employees across departments and roles, including the supply chain team. Your employees in the supply chain department should be able to review the data and provide input based on their outlook and experience.
Avoid Duplicate BOM and Item Information
Finally, your data should have a single master source. An important step or fundamental of BOM management is to avoid duplication. This entails pulling part data from an item master you can update centrally rather than feeding information on a BOM-by-BOM basis. You should then supply the same data to the BOM management dynamically. This allows you to keep the data up to date, improve accuracy, reduce duplication, and ascertain where the parts are used.
Keep Data Current
Keep BOMs Up to Date
You must remember that outdated data is hazardous for BOM management. Outdated data is useless, no matter how accurate it is. You need to ensure that BOM data is up to date. Manufacturers should be confident that the data they require, and access, is the current version. But how do manufacturers ensure that their BOM is the latest version? Moreover, how do they find out what their BOM looked like at a certain point in time if they are compelled to go back to earlier versions to resolve issues?
Here’s how you can ensure that your BOMs are kept up to date.
Put BOMs Under Change Control
You have to keep BOM data under a managed change process. Change management is essential to tracking bill of materials history and revisions. It ensures that whoever accesses the BOM data gets to use the latest design. These users can therefore feel more confident about their work.
Keep Data Centralized and Accessible
An increasing number of companies worldwide are turning to cloud computing to centralize data that is accessible anywhere in the world. Moreover, storing your BOM data on the cloud helps ensure that everyone gets access to the same information as others. An effective measure to incorporate is BOM Que BOM. This management concept guarantees that your production schedules and inventory levels are in sync, keeping data at your fingertips.
Manage Complete BOMs
Following is complete information on BOM management:
Create Complete Product Definitions
Manufacturers use their BOMs to convey the complete product composition with the proper context to others. A bill of materials is not just a CAD structure or an assortment of parts – it is more than that. And although CAD integration is significant, it doesn’t do the job as it does not communicate the whole story. Therefore, you need to ensure that your BOM data carries complete product definitions.
Organize BOM Data by Role
Another important aspect of BOM management is an organization for BOM management. A bill of materials structure sometimes requires modification to provide the right information, as it doesn’t always align with the best format for execution. For instance, you may want to add tooling, consumables, non-modeled parts, etc. Moreover, every person’s perspective varies, which implies that people need different data to perform their roles.
Here’s an example of what that means. A person from the purchasing department may view an assembly as a single item from a supplier, while a designer might model the same assembly with all of its underlying components. Similarly, third-party stakeholders like suppliers may need access rights to only a subset of data. This is why you need to organize data in a way that matches the intended user’s execution requirements.
Create New Knowledge
You can use BOM data to calculate new details, including cost management roll-ups, ordered quantities, weights, etc. It is challenging to do these calculations in spreadsheets because of the way they are organized. Moreover, BOM data can serve as a vital source of profound business insights if you apply business intelligence and machine learning processes. However, the overarching consideration should always be to keep the data in context, as without context, it would be of little help.
Communicate BOM Data Clearly
Focus on Clarity of Communication
A bill of materials is of little use if the people who need it to do their jobs cannot easily understand it. Always bear in mind that a BOM is a communication tool. More often than not, BOMs are merely long lists of numbers that make little sense to others. For instance, utilizing material abbreviation is an effective way of simplifying communication and making the BOM easily understandable for stakeholders.
Here’s how you can ensure that your BOMs are helpful to others.
Create Personalized Data Views
First, people require varying views to utilize the BOM and make it clear. Therefore, it is vital to give role- and task-appropriate data. For example, your supply chain team does not need your part numbers, so you only need to share a portion of the BOM data with them. It is necessary for a bill of materials management.
Present BOMs in a Visual Context
Next, try to ensure the BOM presents information visually and intuitively. A better option would be to choose thumbnails of parts rather than opting for long lists of numbers. It is crucial for a bill of materials management. Similarly, multilevel views are also very valuable as they allow you to expand, contract, flatten, and drill down data to gather insights or access CAD files. It is a more suitable alternative to using indentations and complex colors in spreadsheets.
Consider a flowchart depicting a bill of materials example showing connections between a bicycle’s frame, wheels, and other components. Visual aids like this help improve comprehension and increase the appeal of presentations. A sample bill of materials may also be useful in representing visuals and ensuring everyone involved is on the same page.
Make BOM Data Digitally Accessible Downstream
Another important thing that the BOM management process encompasses is digital access. Lastly, other people and systems need to interpret your data. Therefore, you should make it accessible in a database and not restrict access to it by locking it up in a CAD file or a spreadsheet.
Put BOM Data Into Action
Extend BOM Knowledge to Support Downstream Processes
Effective BOM execution combines data with the BOM management process. It leads to an integrated approach that links the product design from the engineering team with whatever is required to achieve it downstream. Moreover, BOM quantities should always be accessible to other teams for calculating manufacturing quantities and determining procurement requirements. Similarly, you should make BOM data available for decision-making regarding rollups like costs or materials quantities.
Leverage BOM Explosions for Procurement and Production Planning
Best BOM software or BOM solution should also allow BOM explosions to help plan production and communicate demand to suppliers. It should share that information with an ERP system if available. One can also leverage PLM BOM management or PLM BOM for planning
Benefits of Accurate BOM
Quantifying the direct and indirect benefits of accurate BOMs is often an uphill task. However, delineating these benefits is easy.
Here are some of the benefits of accurate BOM management.
Fewer incorrect material purchases
By utilizing the information contained in the BOM to generate purchase requisitions, there is less of an opportunity for guesswork, variation, or errors in the transmission of material requirement data to suppliers.
Faster execution of planned work
When you use accurate EBOMs, it significantly reduces the time you need to spend researching the required materials. This allows you to streamline the planning and procurement processes. As a result, it reduces the time you need to acquire the necessary parts to complete the job. Essentially, it reduces the Bom LT (Lead Time) effective in streamlining workflows and fastening production.
This enables you to perform faster execution of equipment CMs or PMs and lets you bring the equipment back online in a relatively shorter period. Some of the best BOM software can help you with it.
Faster execution of unplanned work
Effective EBOMs also help craftsmen in emergencies by providing quick access to accurate part descriptions or requirements. Provided that your inventory control system is reliable, your craftsmen can quickly ascertain the location of available parts in stock and their on-hand quantities. In case your inventory levels are below optimal, the EBOM can give supplier and manufacturer details to expedite the procurement process.
More effective reliability engineering
EBOMs allow you to identify similar equipment and parts, enabling you to standardize or substitute individual materials where possible.
Conclusion
Effective BOM management is a critical aspect of agile PLM; PLM BOM management can significantly impact the success of product development. The BOM management process is of immense importance for the production of impeccable products. By implementing best practices of bill of materials, BOM management, BOM methods, and PLM BOM management, you can achieve standardization and quality. By implementing best practices such as a standardized BOM structure, BOM DMS, utilizing PLM software, and ensuring cross-functional collaboration and accurate data, teams can improve communication, streamline processes, and reduce errors. We can also use the best bill of material software.
As a result of effective BOM management, you can bring your products to the market faster and with improved quality. By prioritizing BOM management, teams can optimize their product development process and set themselves up for success. Therefore, BOM management and the bill of material itself are essential when it comes to efficient product development.
If you need further assistance managing your PLM BOMs, contact us at [email protected].
FAQ
BOM management refers to a Bill of Materials, a comprehensive list outlining components, materials, and quantities needed for a product.
BOM stands for Bill of Materials, a structured inventory document crucial for production and supply chain management.
BOM management strategy involves optimizing the creation, maintenance, and utilization of Bill of Materials management to enhance efficiency and reduce costs in the production proces
In project management, BOM refers to the Bill of Materials, a detailed inventory of project components, facilitating resource planning and project execution.
A BOM tool is software designed to create, organize, and manage Bill of Materials efficiently, aiding in product development and manufacturing processes.
An example of a BOM management is a list detailing components like screws, bolts, and electronic parts required to assemble a specific product, such as a smartphone.
BOM in PLM is a structured list of components, parts, and materials required to manufacture a product.
In Agile PLM, BOM refers to the Bill of Materials, a comprehensive record of all components and their relationships within a product.
The BOM of a product life cycle encompasses all versions and revisions of a product’s bill of materials throughout its entire lifespan.
To enhance BOM accuracy, ensure regular updates, involve cross-functional teams, use PLM software, and maintain strict version control.